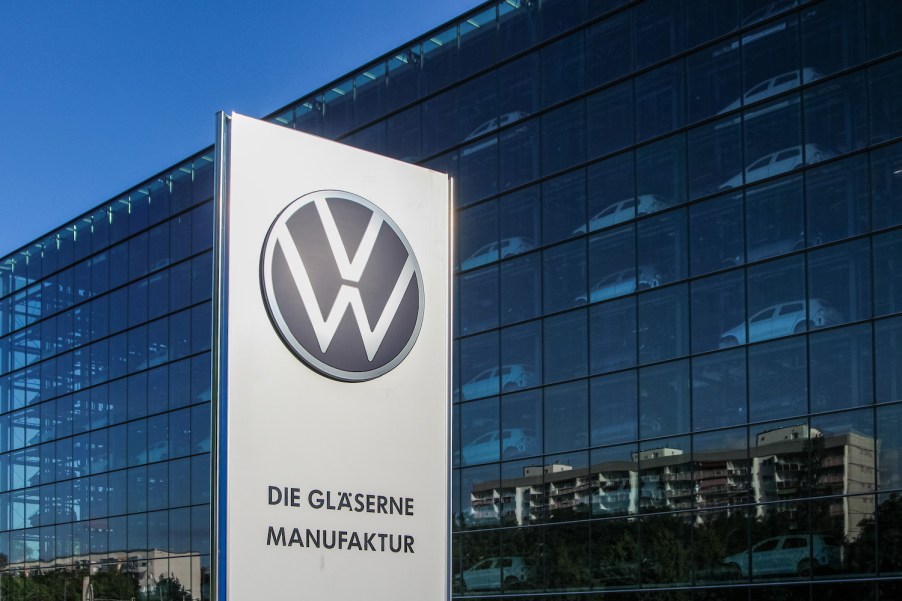
Does Factory Location affect Build Quality?
Carmakers build their products all over the world. In addition to the United States, Ford has factories spread throughout Europe, South America, and Asia. With that scale of production, Ford must uphold acceptable quality control standards. One misplaced part could start a fire, or cripple the braking system. The auto industry goes the extra mile to ensure carmakers uphold certain standards, but sometimes the automakers build cars that aren’t up to snuff.
How do car companies keep up with quality control?

Production cars are based on a prototype, put through various tests. That’s where quality control starts. Once that prototype passes its series of tests, it’s ready for mass production. Of course, the automaker must guarantee the quality is honored throughout each plant building that car. Each factory must comply with industry standards, federal and state laws, as well as company best practices.
What happens when quality control fails?

Several times various issues have fallen through the cracks of quality control. It can be a small issue that becomes a recall, like a defective lamp. Sometimes it’s a much larger, more expensive problem. Automatic transmissions in Ford Fiestas and Focuses from 2012-2016 had a debilitating lurch problem, which caused accidents and led to a class-action lawsuit, lemon-lawing the cars. Volkswagen went through its emissions debacle in 2015 when its cars were tricking smog computers into passing their inspections.
Does factory location affect build quality?

Although assembling cars is standardized to a well-oiled machine, an individual factory can make a difference, for better or worse. GM had a factory in Fremont which was notorious for poor quality control. It closed in 1982. In 1984, GM and Toyota initiated a partnership where both automakers would jointly operate a plant in Fremont, California, called NUMMI. The idea was for GM to learn how to build more advanced cars more efficiently, and for Toyota to have a shot at the U.S. market.
This venture lasted until 2010 when the plant finally closed. Despite problems with marketing Toyota-based GM cars and the United Auto Workers (UAW) union, it wasn’t exactly a failure. GM has since implemented Toyota’s practices and is a world leader in quality and productivity.
Is it possible to trace a widespread problem to a specific factory?

NUMMI was an example of an effort to improve quality control and efficiency, based on a single factory’s practices. That said, quality control comes down to the workers. A VIN says everything anyone needs to know about their car, and if someone wants to find out where their car was built they can easily do so. Unfortunately, in the case of a class-action lawsuit, the specific VINs of affected cars will most likely be kept confidential, so it may not be possible to narrow down a defect to a specific factory.
However, this may not be relevant for all problems. The Takata airbag recall affected 40 million different kinds of vehicles, from 12 different brands. In that case, the recall traced back to the part manufacturer. Other issues, like the premature rust on Toyota 4Runners, may stem from systemic quality control failure.