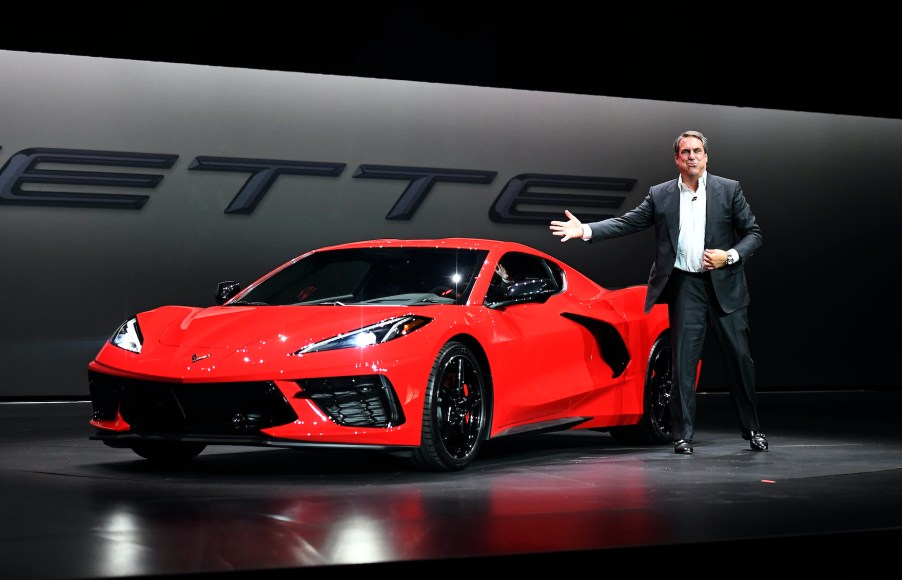
Why GM Built a Chevy C8 Corvette Almost Completely in 3D Printed Materials
3D printing has recently been making an impact on a wide range of industries, including the automotive industry. The ways that automakers such as General Motors have used this manufacturing technique this year are surprising. How has GM put the versatility of 3D printing to work for developing the 2020 Chevy C8 Corvette and beyond? And how crucial will this manufacturing technique be to the auto manufacturing industry moving forward? Roberto Baldwin from Car and Driver provides us with the details.
How GM leveraged 3D printing for the Chevy C8 Corvette . . . and medical equipment
GM was an early adopter of 3D printing. It has been increasingly relying on it to help develop new vehicles since the late ’80s. In the months before the Chevy C8 Corvette‘s launch, the carmaker incorporated the technique—also known as additive manufacturing—into prototyping the first-ever mid-engine ‘Vette.
But there was a big difference between how GM built this particular prototype and others in the past. 75 percent of the first physical prototype of the C8 was 3D printed. This prototype was non-operational, but it did have many mechanical 3D parts for the retractable hardtop. Using these parts, the company was able to fine-tune the feature’s opening and closing functionality.
When COVID-19 gripped the U.S., GM paused vehicle production as did nearly all automakers. But it shifted gears and used its 3D printing technology to assist in providing much-needed personal protective equipment for medical workers. Using this technology, it was able to develop parts for face shields. After getting feedback from the medical community, it retooled quickly and manufactured parts for 17,000 face shields.
Why this technique served GM well
One of the most important advantages of 3D printing is that it enabled General Motors to pivot rapidly and relatively cheaply if a design change was needed. On a macro scale, the carmaker moved from vehicle development and production to making parts for medical equipment in a matter of weeks. Additive manufacturing enabled it to take on a completely different design request and produce the finished product with little disruption.
GM also benefited from the fast turnaround in designing and adjusting parts in the development of the Chevy Corvette C8. Because three-quarters of the C8 was made from printed materials, GM’s design team could easily see how components fit together. Access to different areas of the car to make adjustments was also easier for the team. And 3D printing of parts for the C8 Corvette allowed the team to make modifications as often as necessary.
Having 3D printed components readily available has also helped GM on the production line. They are used in training production robots to learn about access points and buildability.
How automakers will embrace 3D printing in the future
Engineers at GM and other carmakers foresee a time in the future when owners can use an app to download and print parts for themselves via subscription service. But it will probably be several years until home 3D printers have that kind of large-scale capability.
In the meantime, we can expect automakers to use 3D printing for in-house production of tooling equipment. Not only does it greatly reduce the cost of making this equipment but also decreases its production time. Additional benefits include improved ergonomics and productivity on the assembly line.
Offering car owners more customization of parts is another quick, cost-effective way car manufacturers will take advantage of this technology. Recently, according to AMFG, companies such as BMW’s MINI and Volkswagen are offering their customers ways to personalize their cars. Dashboards, liftgates, gear shift knobs, and LED door sills are among the components that owners can buy to make their cars unique.
3D printing technology will also play a significant role in the production of spare parts for vintage cars. Normally, these parts are expensive to produce and the cost is passed on to the owner. But components made from 3D printed materials can be produced relatively cheaply and quickly.
Other possibilities using this technology that car manufacturers might utilize include the production of motorcycles and smaller cars, optimization of parts for race cars, and using 3D prototypes for design validation and function testing.
It’s clear that 3D printing has opened up numerous options in automotive design, development, and production. Engineers in the industry anticipate that there will be even more ways this technology can be harnessed. And if carmakers such as GM, Ford, and Tesla need to retool in order to make more medical equipment in an emergency, they can do it in short order.